Simulation and Optimization of Electric Fields in Electrostatic Flocking
Published Date
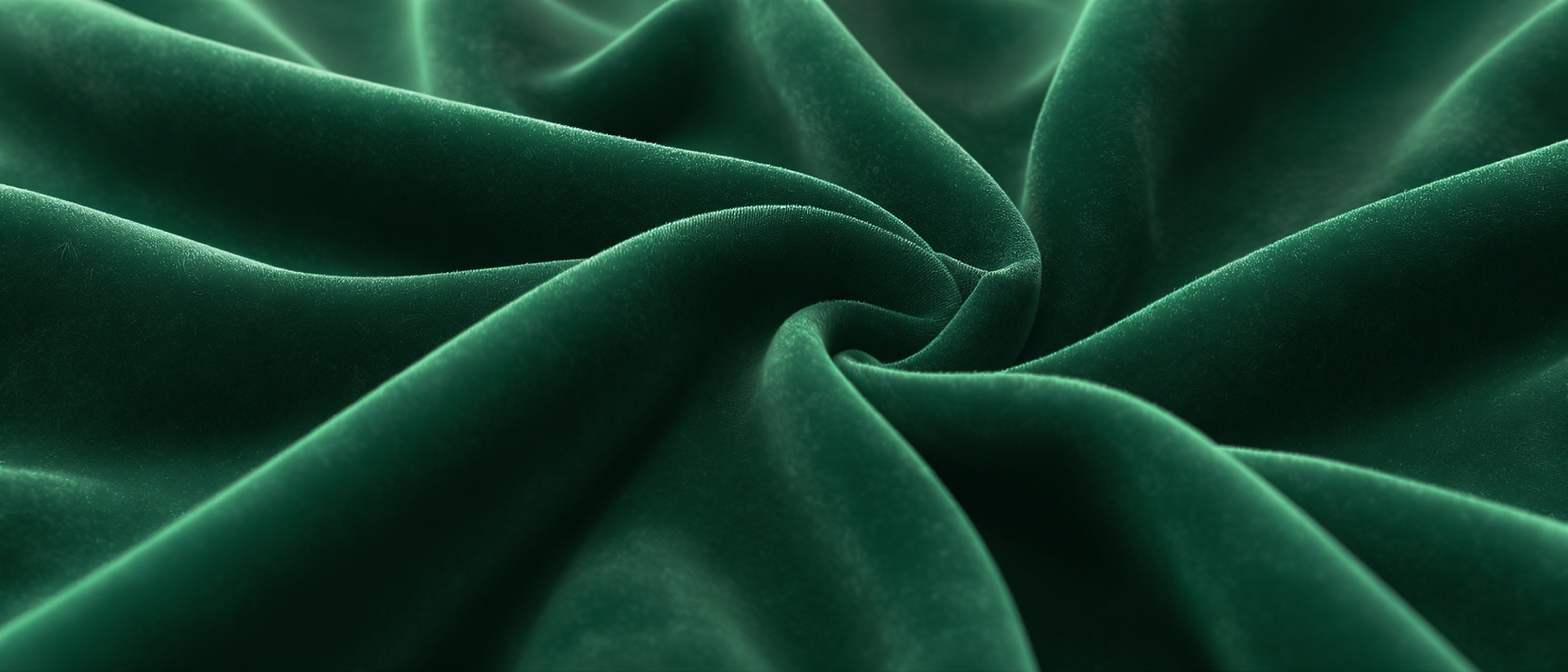
Background
Electrostatic flocking is a production process that utilizes the physical principle of like charges repelling and opposite charges attracting. By establishing a strong electric field through a high-voltage power supply, it drives negatively charged flock fibers to adhere uniformly onto adhesive-coated substrates. This technique features simple processing, low cost, and unique decorative effects (such as velvet-like or embroidered textures), making it widely used in artistic decoration, automotive interiors, packaging, handicrafts, and home textiles. The core process involves multiple physical mechanisms including fiber charging, electric field interaction, and adhesive curing, positioning it as a key technology in surface treatment and decorative applications.
From a physical perspective, the core driving force of electrostatic flocking lies in the electric field distribution generated by the high-voltage power supply. The directional movement, density, and adhesion efficiency of flock fibers are directly influenced by the uniformity, stability, and intensity of the electric field: insufficient field uniformity (e.g., voltage fluctuations) leads to uneven fiber distribution, particularly problematic in mass production of products like flocked wallpapers; field stability (output stability of the high-voltage power supply) determines the consistency of flocking effects; while field intensity (within the 40-60kV voltage range) serves as the critical parameter for optimal adhesion efficiency. Fiber density further affects product appearance, tactile properties, and wear resistance, making precise control of electric field distribution the key to improving flocking quality.
However, current flocking processes face significant challenges: traditional electrostatic flocking and spray flocking suffer from low efficiency, severe fiber waste, and environmental pollution, with particularly prominent energy consumption and material loss in mass production. Meanwhile, issues like uneven fiber distribution and poor adhesion (e.g., on non-polar materials such as PP) caused by non-uniform electric field distribution often result in defect rates of 15%-20%, directly increasing production costs. In this context, simulation and optimization of electric field distribution have become critical technical solutions - by accurately modeling field distribution patterns, targeted optimization of high-voltage power parameters, electrode structures, and material dielectric property matching can be achieved, thereby improving fiber adhesion efficiency and distribution uniformity while reducing defect rates and material waste.
Based on this, the core objective of this report is to systematically review simulation methods for flocking electric field distribution (such as electrostatic field modeling and multi-physics coupling analysis), optimization strategies (including field parameter adjustment, electrode structure design, and material property matching), and practical application challenges (such as complex surface adaptation, energy efficiency, and environmental sensitivity), providing theoretical support and practical references for the technical improvement and engineering application of electrostatic flocking processes.
Basic theoretical system for simulating electric field distribution in flocking
Electrostatic Induction and Charge Coupling Mechanism
During the electrostatic flocking process, the linear relationship between electrode plate charge density and voltage forms the basis for understanding electric field distribution. According to fundamental electromagnetic principles, the electric field intensity (E) between plates is determined by the plate voltage (U) and inter-electrode distance (d) (E=U/d), while the plate charge density (σ) maintains a linear relationship with electric field intensity expressed as σ=ε₀·E (where ε₀ represents vacuum permittivity). This relationship demonstrates voltage's direct regulatory effect on charge distribution across electrodes.
The fiber charging process involves coupled mechanisms of contact electrification and polarization charging. Fibers typically acquire negative charges through contact with the negative electrode (such as a metal mesh frame) while simultaneously undergoing polarization within the electric field: negative charges with the same polarity as the electrode concentrate at the end furthest from the negative electrode, whereas positive charges accumulate at the end nearest to it. Given that electrode materials exhibit significantly higher conductivity than fibers, the fibers ultimately carry a net negative charge. This process not only achieves charge transfer through contact but also enhances charge accumulation via electric field polarization, representing a combined effect of contact electrification and polarization charging.
Electric field distribution directly influences fibers' initial acceleration and motion trajectory. Negatively charged fibers experience compound motion of translation and rotation under electric field forces: translational motion manifests as variable acceleration, with initial acceleration positively correlated to both electric field intensity (determined by plate voltage and spacing) and fiber charge quantity - higher field intensity and greater charge result in faster initial velocity buildup; rotational motion presents as periodic low-damping oscillation with gradually decreasing amplitude until stabilizing in an equilibrium position perpendicular to the plates. These kinematic characteristics enable fibers to straighten and move vertically at high speed, ultimately attaching to adhesive-coated substrates in an upright orientation. Uneven field distribution or insufficient intensity (e.g., voltage below 20kV) significantly compromises fiber vertical alignment, while excessive field strength (e.g., voltage exceeding 100kV) may trigger issues like electrostatic spark-induced fiber burning, further validating the critical regulatory role of electric field distribution on fiber motion trajectories.
Comparison and Selection of Numerical Simulation Methods
In the simulation of flocking electric field distribution, commonly used numerical simulation methods mainly include the finite element method (FEM), boundary element method (BEM), and finite difference method (FDM). These methods exhibit significant differences in principles, applicable scenarios, and computational characteristics, requiring the adoption of a "scenario-adaptive" selection strategy based on specific simulation requirements.
The finite element method (FEM) discretizes continuous domains into elements to solve Maxwell's equations, supporting both two-dimensional (e.g., ELECTRO) and three-dimensional (e.g., COULOMB) simulations. It can handle static, time-harmonic, and fully transient electric fields, making it suitable for simulating electromagnetic field distributions in complex geometries. Its advantage lies in handling nonlinear and anisotropic materials (such as high-voltage bushings, insulators, and other power equipment), while achieving high-precision 3D simulations through techniques like Gmsh tetrahedral meshing, with results verifiable against mature commercial software. However, it should be noted that FEM accuracy heavily depends on mesh quality, with research indicating that mesh size should be ≤1/10 of the smallest characteristic length of the electrode plates to ensure accurate simulation of complex plate structures (e.g., curved plates).
The boundary element method (BEM) reduces computational dimensionality through boundary discretization, requiring only surface meshes rather than volume meshes. It is suitable for simulating electric fields in unbounded domains or large open areas (e.g., transmission tower insulators, open-domain fields in transverse flight methods) and thin-layer problems (e.g., contaminated insulators). Compared to FEM, BEM reduces the number of unknowns, particularly excelling in solving unbounded domain problems like radiation and scattering. However, it cannot handle nonlinear or anisotropic materials.
The finite difference method (FDM) converts partial differential equations into difference equations via grid discretization, making it suitable for dynamic electromagnetic field simulations such as dynamic voltage modulation (e.g., finite-difference time-domain (FDTD) for antenna design and dynamic simulations of photonic crystals). Its principles are straightforward and easy to implement programmatically (e.g., solving electric field equipotential lines through iterative formulas), but it performs poorly with complex geometries and suffers from slow convergence.
In summary, for different scenarios in flocking electric field distribution simulations, a "scenario-adaptive" selection strategy is recommended:
Complex plate structures (e.g., curved plates): Prioritize FEM to address geometric complexity.
Open-domain electric fields (e.g., transverse flight methods): Use BEM for efficient handling of unbounded domain problems.
Dynamic voltage modulation scenarios: Employ FDM (or FDTD) to meet dynamic electromagnetic field simulation needs.
Additionally, special attention should be paid to FEM mesh quality, with a recommended mesh size ≤1/10 of the smallest characteristic length of the electrode plates to ensure simulation accuracy.
Key Influencing Factors and Technical Strategies for Flocking Electric Field Optimization
Impact of Voltage Fluctuations and Dynamic Regulation
Voltage, as the core parameter of the electrostatic flocking field, directly affects flocking quality through its magnitude and stability. Research shows that voltage fluctuations significantly influence fiber flight speed, implantation depth, and distribution uniformity by altering electric field strength. Experimental data indicate a linear relationship between flocking density and voltage variation (Δρ = k·ΔU, k = 2.4%/kV), meaning a 1kV voltage fluctuation results in approximately a 2.4% change in flocking density.
Specifically, when voltage is too low (<40kV), fibers fly slowly with insufficient kinetic energy, making them prone to air resistance and gravity, leading to inadequate flocking density, fiber tilting, or shallow implantation (poor adhesion). Conversely, excessively high voltage (>60kV) causes fibers to fly too fast, potentially disrupting adhesives or coatings due to excessive dispersion, while also increasing the risk of air ionization, resulting in scattered fibers. Voltage stability is equally critical, as fluctuations cause inconsistent electric field strength, leading to uneven flocking density (e.g., inconsistent effects across different areas in large-scale flocked wallpaper production).
To address voltage fluctuation control, two main technologies are currently employed: traditional PID control and intelligent fuzzy control. Traditional PID control is cost-effective (~3000 RMB), using closed-loop feedback (response time <10ms) to compensate for load variations, maintaining ripple coefficient <1% and voltage fluctuations within ±0.5%. However, it has weak anti-interference capability and poor adaptability to complex load changes (e.g., coating thickness deviations >5μm). Intelligent fuzzy control, with custom-developed algorithms (~8000 RMB), achieves higher precision (voltage fluctuations <±1kV) and supports output voltage correction within 0.5 seconds (adjustable from 60-100kV), making it particularly suitable for scenarios with frequent load variations. Additionally, when combined with pulse modulation technology, it precisely controls charge release rates, while IGBT frequency conversion modules reduce energy consumption per unit area by 22%, further optimizing control performance.
Given varying application requirements, a "scenario-based" control strategy is recommended:
Standard flocking (e.g., conventional wallpaper, basic industrial products): Prioritize cost-effective PID control to balance economy and basic quality requirements.
High-precision applications (e.g., automotive interiors, precision electronic component flocking): Adopt intelligent fuzzy control to ensure uniform fiber alignment, strong three-dimensional effects, and consistency.
Humidity Interference and Compensation Methods
Environmental humidity is a critical factor affecting the distribution of electrostatic flocking fields and flocking effectiveness. Its interference mechanisms and compensation techniques require multi-dimensional analysis involving charge characteristics, electric field distribution, and material properties.
Mechanisms of Humidity Interference
Environmental humidity interferes with the flocking process in the following ways:
First, increased humidity causes a water film to form on the fiber surface, accelerating charge dissipation. Additionally, higher moisture content in the air neutralizes surface charges on fibers, significantly reducing their flight capability and adhesion efficiency, ultimately leading to sparse flocking. Experiments show that for every 10% increase in humidity, fiber surface charge decay intensifies, potentially causing up to a 25% deviation in flocking density.
Second, humidity variations alter the dielectric constant of air, directly affecting the electric field distribution between parallel electrode plates. When relative humidity exceeds 70%, condensation on insulating medium surfaces forms liquid films, further modifying dielectric properties and exacerbating uneven electric field distribution.
Third, humidity significantly impacts adhesive performance and fiber condition: high humidity slows adhesive drying and reduces tackiness, weakening flocking adhesion. Meanwhile, when fiber moisture regain is below 8%, fibers exhibit poor lift-off and residual loose fibers, whereas exceeding 8% leads to excessive and irregular motion speed, causing fiber shedding.
Humidity Interference Compensation Technology
From the perspective of the compensation mechanism, the polarization relaxation time of water molecules is approximately 10⁻⁶ s. Under the influence of a high-frequency electric field (50–100 kHz), water molecules rapidly complete the polarization process, reducing their neutralizing effect on the surface charges of the fibers, thereby stabilizing the electric field distribution and fiber trajectories.
In terms of technical implementation, humidity sensors with an accuracy of ±2% RH are installed around the open electrode plates to monitor local micro-environmental humidity in real time. Meanwhile, based on a humidity compensation model, the output frequency of the high-voltage power supply is dynamically adjusted (switching within the 50–100 kHz range) to adapt to humidity fluctuations. Experimental verification shows that this solution can effectively reduce the deviation in flocking density caused by humidity interference from 25% to 5%. Additionally, multiphysics simulation technology can further optimize the compensation effect: by establishing a liquid film thickness-dielectric constant model or using fluid dynamics software to simulate the temperature and humidity distribution of the liquid film, more precise parameter support can be provided for electric field compensation strategies.
To ensure overall flocking quality, ambient humidity should be maintained within an optimal range (recommended 40%–60%). When the relative humidity exceeds 70%, an electrode dehumidification module should be activated to prevent additional interference from liquid films on the electric field.
In summary, by combining the high-frequency electric field compensation mechanism with local micro-environment control technology, the interference of environmental humidity on the electric field distribution during flocking can be effectively reduced, improving the stability of flocking density and adhesion.
Optimization Design of Electrode Structural Parameters
Optimizing the design of electrode plate structural parameters is a core step in improving the uniformity of the electrostatic flocking field and flocking quality. It requires comprehensive consideration of the synergistic effects of electrode distance, voltage, and material properties, along with dynamic control and structural innovation strategies.
First, electrode distance and voltage are key parameters affecting electric field strength, and their optimization requires constructing a three-dimensional "distance-voltage-material" model based on fiber material characteristics. The electrode distance (gap between plates) directly influences electric field strength. Experiments show that flocking density is inversely proportional to electrode distance, with a critical distance beyond which flocking becomes impossible. In practice, the inter-electrode spacing is typically maintained at 6–10 cm (60–100 mm). However, excessive spacing weakens the electric field, reducing fiber flight efficiency, while insufficient spacing risks electric breakdown. Different fiber materials (e.g., viscose, nylon) exhibit varying sensitivities to distance and voltage: for nylon fibers, voltage has a greater impact on flocking density than distance (priority order: fiber length > plate distance > fiber fineness > plate voltage), whereas for viscose fibers, distance plays a more significant role (priority order: fiber length > plate voltage > plate distance > fiber fineness). Based on this, the 3D optimization model provides specific parameter recommendations for viscose fibers: 60–80 mm electrode distance and 50 kV voltage to balance field strength and flocking effectiveness.
Second, electrode plate structural design is crucial for optimizing field uniformity. Traditional flat plates achieve only 80% field uniformity, whereas custom 3D-printed curved plates (e.g., parabolic) can increase uniformity to over 95%, significantly improving fiber charging and trajectory. Additionally, plate geometry (e.g., mesh, grid, or flat) strongly influences fiber distribution: mesh or grid upper electrodes (metal frames) prevent fiber bridging, promoting uniform distribution and directional flight, while parallel flat electrodes—prone to bridging—are suitable only for single-sided processing. For complex surfaces (e.g., automotive interior contours), multi-electrode array systems (16-channel independent voltage control, ±5% precision) compensate for edge field strength variations, addressing uniformity challenges in irregularly shaped components.
Finally, the dynamic electrode plate design employs a closed-loop control system with servo motors and laser distance measurement (response time 20ms) to adjust the electrode distance in real time according to different material or surface requirements, further enhancing electric field stability. This solution integrates curved plates with multi-electrode array technology, forming a complete technical chain from parameter optimization to dynamic control, effectively supporting high-precision and high-uniformity production in flocking processes.
Analysis of Electric Field Compatibility for Different Flocking Processes
The electric field adaptability of flocking processes requires targeted optimization based on fiber movement direction, equipment characteristics, and substrate requirements. Currently, mainstream flocking processes can be categorized by fiber movement direction into descending, ascending, and horizontal flying methods, each with distinct electric field distribution characteristics and optimization needs, as analyzed below:
Descending Method: The most widely used process in China (over 80% adoption), it employs an upper electrode made of a metal mesh frame and a lower electrode as a flat metal plate. Fibers are charged and polarized during descent, with electric field strength determined by plate voltage (U) and plate distance (d). The optimal voltage range is 40–60 kV—too low results in sparse fibers, while excessive voltage may damage adhesives or coatings. Simulations show a significant edge field gradient (ΔE = 10 kV/m) in this method, necessitating edge shape optimization for improved field distribution. Additionally, fibers move vertically under electric and gravitational forces, exhibiting variable-acceleration translation and low-damping vibration. Optimizing insertion angles requires controlling field strength and charge levels, making this method suitable for flat flocking products (e.g., wallpaper, fabric).
Ascending Method: Fibers move upward into the substrate, traditionally suffering from uneven flocking. Improved versions enhance uniformity via yarn rotation. Since gravity must be overcome, higher field strength is required (recommended voltage 10% higher than descending methods), with voltage stability directly affecting flocking uniformity and current stability influencing charge release consistency. Fiber trajectories are influenced by electric force, gravity, and air resistance, increasing control complexity. This method is mainly used for high-uniformity specialty products (e.g., yarn flocking).
Horizontal Flying Method: Fibers move laterally into the substrate, requiring specialized electrode structures and voltage parameters. Due to horizontal movement, electric field exposure time must be extended (recommended plate length increased by 20%). Fiber trajectories are susceptible to airflow and field non-uniformity, necessitating precise field optimization via simulation. This method is primarily for specialized horizontal flocking applications (specific use cases under study).
By equipment type, flocking processes include conveyor-based, chamber-based, and nozzle-based systems, each requiring tailored electric field parameters (e.g., field strength, exposure time) to match substrate properties (conductivity, surface shape) and production needs. Conveyor systems suit continuous production (e.g., flocked fabrics, synthetic leather) with stable uniform fields; chamber systems enable rapid flocking (3–5 seconds) for small products via high-voltage fields; nozzle systems apply high-voltage static electricity through nozzles for irregular surfaces.
Specialized processes like 3D flocking (handheld devices for irregular parts), electrostatic-pneumatic flocking (combining electricity and airflow for complex shapes), and horizontal electrode-mechanical feeding (for rotationally symmetric parts) require adjusted field parameters (voltage 20–100 kV, current, flocking time) to meet density, uniformity, and adhesion needs across fiber materials (cotton, viscose, nylon) and substrates (plastic, wood, leather).
For non-polar materials (e.g., TPU, engineering plastics, PP), surface plasma treatment (corona value 38–42 dyn/cm), conductive additives, or PP flocking primers enhance polarity and roughness. Optimizing electrostatic parameters and adhesive application can improve nylon/polyester fiber adhesion on complex surfaces to 98.6%. For composites (e.g., carbonized cotton + carbon fiber), electric fields enable vertical fiber alignment for specialized applications like heavy oil cleanup.
Optimization Effect Evaluation and Verification System
Quality and Cost-Effectiveness Indicators
This chapter establishes a dual-dimensional "quality-cost" evaluation model to systematically analyze key indicators and assessment methods for both quality and cost-effectiveness in flocking optimization processes, providing quantitative criteria for selecting optimal solutions.
Quality indicator system
Quality indicators primarily cover three dimensions: physical properties, structural characteristics, and appearance/tactile feel.
For physical properties, core metrics include abrasion resistance (≥12,000 cycles tested via the Taber method), anti-static performance (surface resistance ≤1×10⁹Ω), and hydrophobicity (contact angle >120°). These indicators directly reflect product functionality and durability, with experimental data confirming that optimized flocking products consistently meet these requirements.
Key structural characteristics include flocking density (flock quantity per unit area or coverage ratio), uniformity (consistent density across regions, with ±2% precision via microscopy or optical testing), adhesion strength (depth of fiber insertion into adhesive, shedding rate—e.g., nylon/polyester fibers achieve 98.6% adhesion compliance on complex surfaces), and upright fiber ratio. Flocking density can be predicted using a multiple linear regression model, with strong alignment between theoretical and measured values.
For appearance and tactile feel, fiber density directly impacts visual and tactile quality. Optimizing atomization parameters (0.4–0.6 MPa pressure at 200 mL/min flow rate, voltage <80 kV) reduces coating thickness standard deviation from 12.3 μm to 4.7 μm, significantly improving uniformity. Color difference control requires standardized raw material batches, dye compatibility, and post-treatment additives.
Economic performance indicator system
Economic indicators focus on energy consumption, cost, and environmental benefits. In terms of energy consumption, the introduction of IGBT frequency conversion modules and intelligent electric field control algorithms can reduce energy consumption per unit area by 22%, significantly improving energy efficiency. Regarding cost, while electrostatic flocking technology initially involves high equipment investment and technical requirements, improvements in production efficiency (e.g., reduced trial runs and lower energy consumption) enabled by high-efficiency high-voltage power supplies, along with simplified processes (requiring only steps like adhesive application, flocking, and drying), can substantially lower long-term production costs. A real-world case study showed that a wallpaper factory saved 120,000 yuan annually after upgrading, with a payback period of approximately 0.4 years.
In terms of environmental benefits, compared to traditional processes, electrostatic flocking reduces the use of chemical solvents, resulting in a more eco-friendly production process and further lowering hidden environmental costs.
A comprehensive evaluation suggests prioritizing optimization solutions that achieve "quality improvement >10% with a payback period <1 year," balancing significant quality enhancement with reasonable economic investment to ensure the sustainability and practical value of technological upgrades.
Comprehensive Verification and Iterative Optimization
The comprehensive verification and iterative optimization process for simulating and optimizing the electric field distribution in flocking can be achieved through a three-stage validation process: "simulation, pilot production, and mass production." Each stage forms a closed loop through data feedback and technical optimization, ultimately ensuring stability in mass production.
First Stage: Digital Twin Simulation Verification.
This stage focuses on finite element simulation (FEM) as the core, verifying simulation accuracy through numerical simulation and experimental comparison. For example, error analysis is conducted using demonstration instruments to observe fiber movement phenomena and analyze the impact of paper debris shape on experimental results, ensuring simulation errors are controlled within 10%. Furthermore, the finite element 3D algorithm is validated through simple test cases (e.g., inner conductor potential at 1V, outer conductor at 0V, with an intermediate dielectric layer). The correctness of the simulation model is confirmed by comparing Gmsh tetrahedral mesh partitioning results with those from mature commercial software. In melt-blown electrospinning simulations, the relationship between fiber descent speed, electrostatic force, and viscosity aligns with experimental results, validating the reliability of the simulation method. By analyzing and improving error sources between simulation and experiments, simulation accuracy is effectively enhanced, providing reliable preliminary support for subsequent stages.
Second Stage: Small-Batch Pilot Production Verification.
Based on digital twin simulations, small-scale pilot production of 500m² is conducted, focusing on verifying flocking density uniformity and qualification rate (target ≥98%). Experimental validation methods include orthogonal design, variance analysis (e.g., analyzing differences in influencing factors between nylon and viscose fibers), and multiple linear regression models (where theoretical expressions fit well with measured values). Additionally, the development of new yarn flocking devices (e.g., rotating grinding wheels driving yarn rotation) improves uniformity. Microscope observations of cross-sections and surface structures compare pre- and post-improvement effects, while pre-baking (75–85°C, 1.5 min) and curing processes fix the fibers, achieving initial iterative optimization. Moreover, an electrostatic flocking fiber flight performance tester measures the time for fibers to fully lift in the electric field, evaluating flight performance and providing data support for quality stability verification and production process optimization. A closed-loop feedback system integrated with machine vision monitors flocking density in real time, further ensuring quality control during the pilot production stage.
Third Stage: Production Line Modification and Mass Production Optimization.
Based on pilot production data, production line parameters are adjusted (e.g., fine-tuning electrode spacing by ±2mm) to achieve mass production stability (≥99% qualification rate for three consecutive batches). During production line modification, the intelligent control system tracks key parameters such as film thickness in real time, forming a closed-loop feedback with the power module to correct parameters within 0.5 seconds. Meanwhile, continuous improvement measures, such as introducing new equipment and optimizing processes, enable precise control of curing temperature and time, enhancing quality stability. The closed-loop feedback system integrated with machine vision and PID algorithms dynamically adjusts electric field parameters (e.g., voltage, electrode spacing), reducing defect rates to within 0.3‰. For uneven flocking on materials like PP plastic, iterative optimization is achieved through surface pretreatment and process parameter adjustments. Additionally, constraint-driven optimization algorithms (e.g., genetic algorithms, particle swarm optimization) combined with environmental constraint modeling (e.g., wind speed compensation) further enhance process stability in mass production through experimental/simulation validation.
Through the synergistic effect of the three-stage validation process, simulation, pilot production, and mass production data form effective feedback, driving continuous improvement in the optimization of flocking electric field distribution. Ultimately, the goal of high stability and high qualification rates in mass production is achieved.
Conclusions and Future Prospects
Existing research has systematically elucidated the electric field principles in electrostatic flocking and achieved multidimensional analysis of electric field distribution through numerical simulation methods such as finite-difference time-domain (FDTD), finite element method (FEM), and boundary element method (BEM). Experimental and simulation results confirm that electric field parameters (e.g., voltage) and environmental humidity significantly affect flocking quality. Additionally, applied technologies such as energy-saving strategies based on quadcopter drones and surface treatment methods for PP materials have shown preliminary progress. However, current research still exhibits notable limitations: models often oversimplify environmental factors (e.g., temperature, humidity) and focus excessively on theoretical simulations, lacking sufficient validation in industrial production. Numerical simulation methods (e.g., finite difference method) struggle with complex geometric structures, and the trade-off between mesh density and computational efficiency remains unresolved.
Based on the current research landscape and technological bottlenecks, combined with trends identified in the literature, future efforts should prioritize the following three research directions:
1. Multi-physics Coupling Simulation Optimization: Current electric field simulations primarily focus on single-field analysis, neglecting the coupled effects of air resistance (flow field) and Joule heating (thermal field) during fiber movement, leading to significant simulation errors. Future studies should integrate electric-field-flow-thermal coupling models, incorporating dynamic environmental factors like temperature and humidity to improve simulation accuracy (target error <5%). Additionally, enhanced meshing techniques (e.g., unstructured grids, adaptive meshing) or multigrid methods could address computational efficiency challenges in complex geometries.
2. Intelligent Electric Field Control System Development: Electrostatic flocking is evolving from a single-process technique to an intelligent system. Future work should develop deep learning-based adaptive algorithms, leveraging over 100,000 datasets (covering electric field parameters, material properties, environmental conditions, etc.) to enable "one-click optimization" of field parameters. Integrating real-time machine vision monitoring could dynamically adjust high-voltage power supply outputs (e.g., via intelligent control and novel topology power supplies), enhancing field stability and flocking quality.
3. Low-Dielectric-Loss Electrode Material Development: Current electrode materials suffer from high dielectric losses, leading to excessive energy consumption. Future research should focus on developing low-dielectric-loss materials (e.g., ceramic matrix composites) to reduce energy consumption by over 20%. Additionally, exploring carbon nanotube-doped conductive fibers (conductivity increased by three orders of magnitude) combined with 100μs-level pulsed high-voltage technology could advance traditional flocking toward high-value-added, nanoscale precision applications.
Furthermore, the application scope of electrostatic flocking can expand by integrating processes like spray printing, embossing, and foaming to develop composite products, as well as exploring novel applications such as yarn flocking. Innovations in branding, design, marketing, and management mechanisms can enhance global competitiveness. Continued advancements in high-voltage power supply technology (e.g., novel topologies for improved conversion efficiency) and cross-disciplinary integration (e.g., dielectric barrier discharge for surface modification) will provide new momentum for the intelligent and sustainable development of flocking technology.