Analysing disturbing noises through friction tests
Published Date
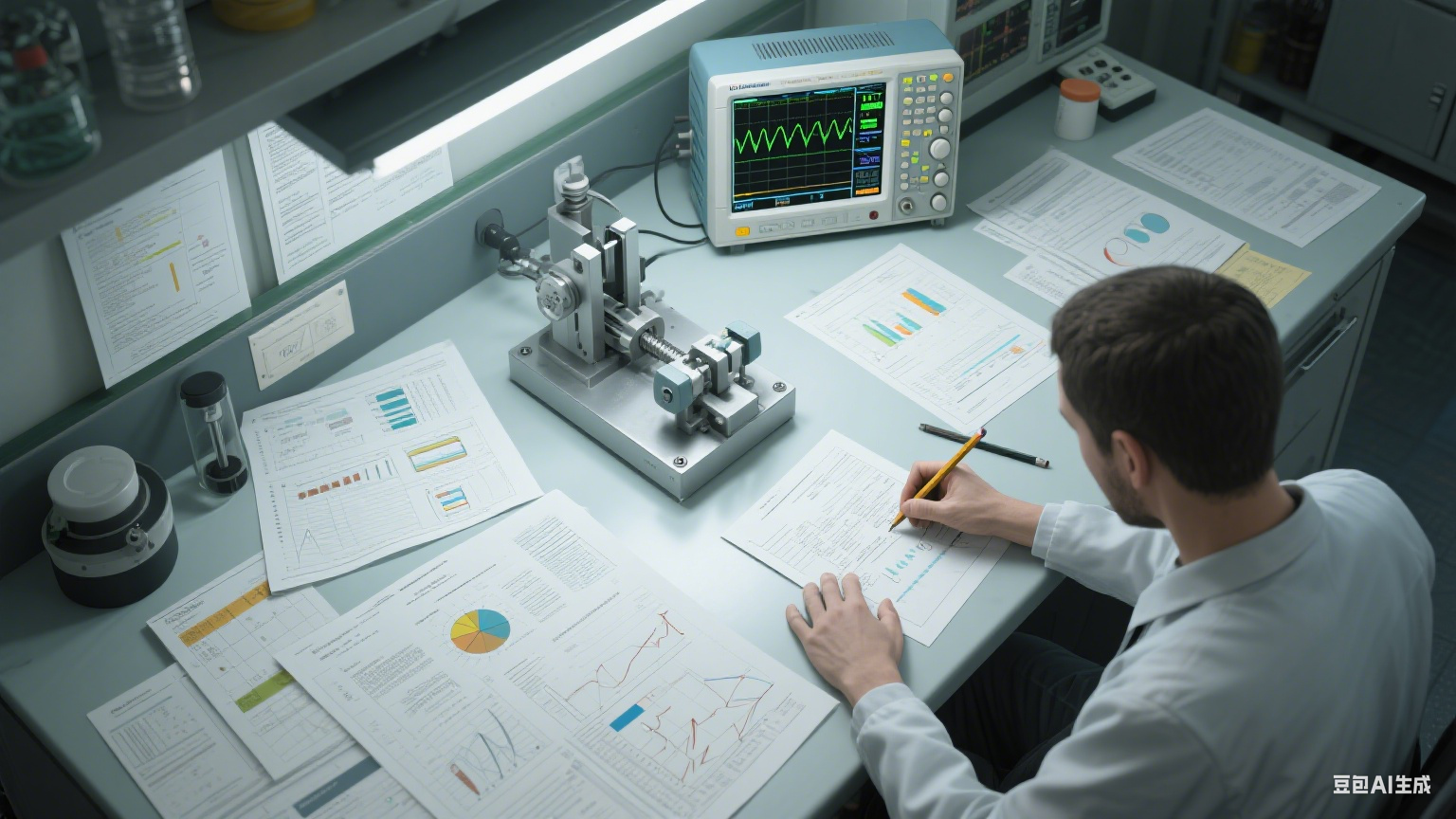
Description
The flocking of sealings to minimize the frictional forces in the contact is a common method in sealing technology. Flocked seals are commonly used in automotive, for doors, glove boxes, hat racks, and storage compartments. They have a great influence on the perception of the quality of the vehicles by the vehicle passengers.
Today‘s customers demand that, for example, moving door windows slide almost frictionless and noiseless. Despite the optimizations made in this area, under certain mechanical and climatic conditions, unwanted friction-induced noise phenomena repeatedly occur in the contact of the seals. The lecture should address this scientifically and economically significant problem and provide results through systematic, friction-based analyses, which characterize the flocked seal as a source of noise. So far, it is unknown what effects the characteristic of the flock and the properties of the friction partner have on the friction behaviour.
Creaking or squeaking are everyday phenomena and regarded as negative noise. Especially in the automobile sector often unpleasant noises are perceived. Seals, which are installed in the vehicle interior, are in many cases the sources of noise of such phenomena. These seals are structural elements, which prevent the unwanted mass transfer of fluid media as well as the contact of other construction elements, such as door and vehicle body due to their damping effect. Consequently, window and door seals on the vehicle contribute significantly to the driving comfort of a car.In addition to the unpleasant perception of wind noise and poor closing behavior of the doors, elastomer seals are often the source of unpleasant creaking or squeaking noises.
This increased noise emission at the contact points can be explained by friction physics and is based on the expression of the stick-slip effect in the contact point. The stick-slip-effect is responsible for this material behavior and forms the focus of the analyzes. Due to the increase in customer complaints about unwanted noise in the vehicle interior, there is an increased need for the analysis of this effect due to economic and scientific aspects. The stick-slip-behavior of a seal is caused by the combination of various properties: The deformability, the surface properties, the climatic conditions in the friction system seal and counter material and the contact conditions, which are defined by normal force or pressure and relative speed. The determination of the friction properties of complex geometries requires a realistic representation of the installation situation of the sample pairing on the laboratory test bench. Only in this case it is possible to take influencing factors into account and to obtain realistic characteristics. For the installation situation, mainly the materials and their sample geometries are decisive. The real 3D profiles of the gaskets must always be used for testing, as the sample shape has a decisive effect on the formation of the friction behavior. Furthermore, unevenness, bends of the counter material and the angle of the seal to the counter material contribute significantly to the deformation behavior of the elastomer sample and thus to the resulting frictional force. Simplification to simple, flat sample geometries is not possible. The influence of the sample geometry can also be extended to the pressure distribution along the sealing edge. Due to strong fluctuations in the distribution, usually due to changing sample cross-sections or different angles of incidence, instability in the friction behavior can occur. Therefore, especially in the field of strongly changing geometries in the vehicle, for example on curved pieces of the sealing tube around the vehicle door, there is an increased risk of creaking. The main factors influencing the formation of the stick-slip of seals with regard to the test conditions are the climatic conditions and the relative speeds of the friction partners. The determined relative speeds are below 1 mm/s up to 125 mm/s. The main part of the real speeds can be found between 1 mm/s and 10 mm/s. The dependence of the frictional force on the speed, which can be explained with the Stribeck curve, has also been demonstrated in the friction test on complex seal geometries. Very low speeds usually lead to stick-slip effects, very high ones lead to higher frictional forces.
The influence of climatic conditions, temperature and humidity could be proven. The temperature here has a complex influence. On the one hand, the formation of the temperature in the friction zone via flash temperatures has a speed-dependent effect on the material properties in the contact region. On the other hand, the ambient temperature affects the entire sample and thus the entire friction system. It could be determined that the frictional forces increase with increasing ambient temperature. This can be explained by a temperature-induced loss of rigidity and thus an increase in the contact area. In addition to changing the frictional forces, the moisture also has an influence on the creaking behavior. An increase in humidity initially leads to a continuous increase in frictional force. The formation of the adhesive force is supported due to the increased adhesion with increasing humidity. This reaches a maximum and it occurs steady stick-slip. If the moisture content is increased further, it will eventually lead to an opposite effect. The amount of moisture then becomes so great that a lubricating film can form. This leads to a decrease in the frictional force and to a continuous, stick-slip-free friction curve. This influence depends on the chemical composition of the surfaces of the friction partners. Depending on the composition hydrophobic or hydrophilic surfaces may be present which influence the distribution and the shape of the moisture molecules. For the influence factor of the roughness a nonlinear dependence could be proven. This is pronounced in each case depending on the roughness of the counter-material. Similar roughness lead to the formation of a high contact surface and to an increase in the frictional force. Large differences between the roughness of the friction partners reduce the contact surface. However, the friction forces do not necessarily have to drop. These changes depending on the deformability of the roughness hills. Considering the travel distance to the first loss of contact of the seal to the counter material is an important parameter to interpret for the risk of gasket creaking. If very large travels can be bridged without loss of contact, the seal will cause no creak even in the automobile. It is possible to distinguish different finishes or flocking on compact specimens. However, it is not possible to examine their tendency to squeak on simplified forms. The determination of the tendency to squeak is crucially associated with the deformation capacity of the seals. A preselection of a coating is thus difficult. As a rule, coatings with low coefficients of friction will also tend less to stick-slip. The influence of the normal force or in the case of complete geometries the influence of the pressure leads in each case to a different expression of the contact surface. The height of the contact surface correlates with the increase in frictional force. In some cases, the distance to the first loss of contact is increased by increasing the friction force, so that the creaking effect can be avoided in a real installation situation. Here the influence of the manufacturing tolerances must be considered. Too small gaps lead to high pressures and thus possibly to stick-slip. On the other hand, excessively large gap dimensions mean that the seals can no longer fulfill their main task of sealing effect. Therefore, it is understandable that high-quality automobiles usually have lower creaking problems due to lower tolerance limits.
The stick-slip-behavior of a seal is always associated with the deformation. Low deformation materials usually have lower coefficients of friction. If anti-friction coatings or flockings are not adapted to it, the deformation can exert a significant influence on the friction behavior. The travel distances in the automobile are relatively low for the seals tested. However, there are a variety of applications that have higher travel distances. It was possible to extract distances of up to 5 mm from relative movement profiles. If, on the other hand, the movement of a side window along a seal is considered, much longer distances are to be included in the analysis. In any case, these exceed the deformation capacity of the seal, so that a coating in the form of a varnish or a flock must be used to reduce the frictional forces and to reduce the wear. With the help of the predictive model, with knowledge of the boundary conditions and with determination of characteristics of the contacting materials, relatively reliable estimates of the risk of creaking can be made. Likewise, the detailed consideration of the resulting classification tree underlines the described influences on the friction behavior. Linear or sinusoidal movements are sufficient for a basic classification of the creaking and friction behavior. The choice of a stochastic profile is recommended for durability and wear tests. Thus, the combination of knowledge about the influences on the creaking and friction behavior, their safe determination and the possible prediction forms the basis for further research activities in this field.

Frictional contact flocked seal, schematic
This article is reprinted with permission from the European Flocking Association. Unauthorized secondary distribution is prohibited