Introduction to Flocking Process Raw Material - Flock Fiber
Published Date
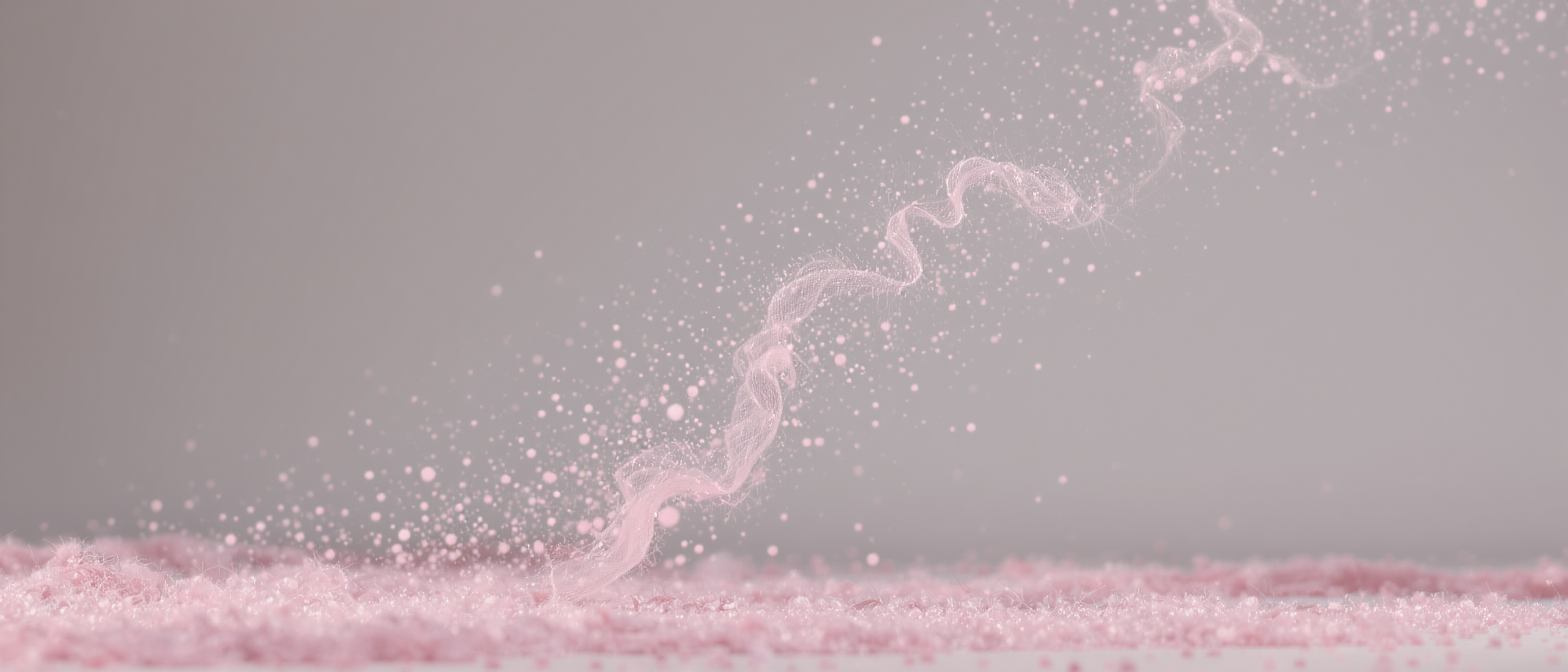
In the flocking process, as the core raw material, the quality and characteristics of flock fibers play a decisive role in the appearance, texture, durability, and other aspects of flocked products. With the widespread application of flocking technology in clothing, home textiles, crafts, automotive interiors, and many other fields, understanding and selecting flock fibers appropriately has become particularly important.
Types of Flock Fibers
Flock fibers are commonly categorized by material into viscose fiber flock, nylon fiber flock, acrylic fiber flock, polyester fiber flock, and cotton fiber flock.
Viscose Fiber Flock
Viscose fiber flock is produced through chemical processing using wood as the raw material. Its fibers have a high crystalline region, making dye penetration difficult, so special dyes and methods are required for dyeing. For example, achieving a deep black shade is challenging. Its polymerization degree is relatively low, resulting in lower fiber strength compared to materials like nylon. However, viscose fiber flock does not soften or melt at high temperatures; it begins to discolor and decompose at 260–300°C, exhibiting good heat resistance. Common dyes such as direct, reactive, and sulfur dyes are suitable for viscose fibers, providing a wide range of color options. It has a soft texture, good moisture absorption, dyeability, and thermal conductivity, with various fineness options to meet diverse needs. However, viscose fiber flock also has drawbacks, such as being prone to fingerprints and lacking resilience.
Nylon Fiber Flock
Nylon fiber flock is a high-molecular-weight material formed by linking organic dicarboxylic acids and diamino acids or caprolactam through amide bonds. It has excellent elasticity, strength, and abrasion resistance and is a thermoplastic fiber. Common types include nylon 6 and nylon 66. Nylon 66 yellows at 150°C, becomes sticky and softens at 230°C, and melts at 250°C, while nylon 6 softens at 180°C and melts at 215°C. Nylon fiber flock offers good color fastness, high yield, excellent three-dimensional effects, and easy dyeing and handling, but it is relatively costly.
Acrylic Fiber Flock
Acrylic fiber flock is stiff, wrinkle-resistant, and highly insulating, with an appearance and texture similar to wool. It has excellent light and weather resistance, losing only 20% of its strength after a year of sun exposure. Acrylic fiber flock dyes brightly, resists fading, and has good chemical stability, resisting acids, oxidants, and organic solvents. However, it has poor moisture absorption, can feel stuffy when worn, and is prone to static and dust accumulation.
Polyester Fiber Flock
Polyester fiber flock is strong, elastic, stiff, wrinkle-resistant, and shape-retaining. It dries quickly after washing without deformation and requires no ironing. Its light resistance is second only to acrylic, and it has strong corrosion resistance, resisting mold and insects. However, polyester fiber flock has poor moisture absorption, can be uncomfortable to wear, and is prone to static and dust accumulation. It also has poor dyeability.
Cotton Fiber Flock
Cotton fiber flock is soft, with good moisture absorption and insulation. It is natural, eco-friendly, and minimally irritating to the skin. However, it has weak abrasion resistance, poor color fastness, difficulty in achieving bright colors, and relatively inferior texture. It also struggles to meet environmental standards. Due to its low cost, cotton fiber flock is commonly used in non-woven short-pile fabrics for black and white products, mainly for EVA-backed flock or lining fabrics.
Flock Specifications
Flock specifications mainly refer to length and fineness, which must maintain a proportional relationship. Imbalance can make it difficult to produce qualified flocked products.
Fiber fineness is typically measured in denier (D), while length is measured in millimeters. Denier is the weight in grams of a 9,000-meter-long fiber; the lower the denier, the finer the fiber. Common flock lengths range from 0.3 to 4 mm, with fineness between 0.8 and 25 D. For example, in flock printing and transfer flocking, manufacturers usually select fibers with lengths of 0.3–1 mm and fineness of 0.8–3 D. If the fibers are too fine and long, they may tangle and fail to penetrate the adhesive layer deeply during flocking. Conversely, short and thick fibers result in a rough surface, losing the flocking style and advantages.
Selection and Pretreatment of Flock Fibers
Selection Criteria
1. Based on Product Requirements: Different products require different flock properties. For example, abrasion-resistant products may use nylon or polyester flock, cost-effective products may use viscose flock, and warmth-focused products may use acrylic or cotton flock.
2. Quality Indicators: Beyond length and fineness, flock quality depends on conductivity, liftability, dispersibility, and uniformity. Good conductivity ensures even charging and adhesion during electrostatic flocking. High liftability allows fibers to rise quickly and vertically in an electric field. Good dispersibility prevents tangling, ensuring even flocking. High uniformity results in a smoother, more attractive surface.
3. Dryness: Moisture adversely affects flocking, so fresh, dry flock should be selected and stored in a ventilated, dry place. In humid environments, fibers absorb moisture, reducing conductivity and liftability, which impacts flocking quality.
Pretreatment Methods
1. Dyeing: Dyeing is critical in flocking. Dyed flock must meet color and physical/chemical standards. Colors must match and remain stable during curing. For printed flock, dyes must withstand steaming, washing, and acid/alkali conditions. For discharge printing, dyes must be reducible to ensure consistent whiteness.
2. Electrification: This process charges the fibers for better adhesion in an electric field. Uniform charging is essential to avoid uneven flocking.
3. Screening: Screening removes impurities, uneven fibers, and tangled clumps. Equipment like vibrating screens or air separators can sort fibers by length, fineness, and weight to ensure quality and uniformity.